Spatial
Andrew Barrie Lab 12 Kanade Konishi Matt Liggins Studio 3 Ruamoko Solutions Watari-Ago Shelter
-
Pou Auaha / Creative Directors
Kanade Konishi, Andrew Barrie
-
Ngā Kaimahi / Team Members
Matt Liggins, Cass Goodwin -
Client
Kaipara Coast Sculpture Garden
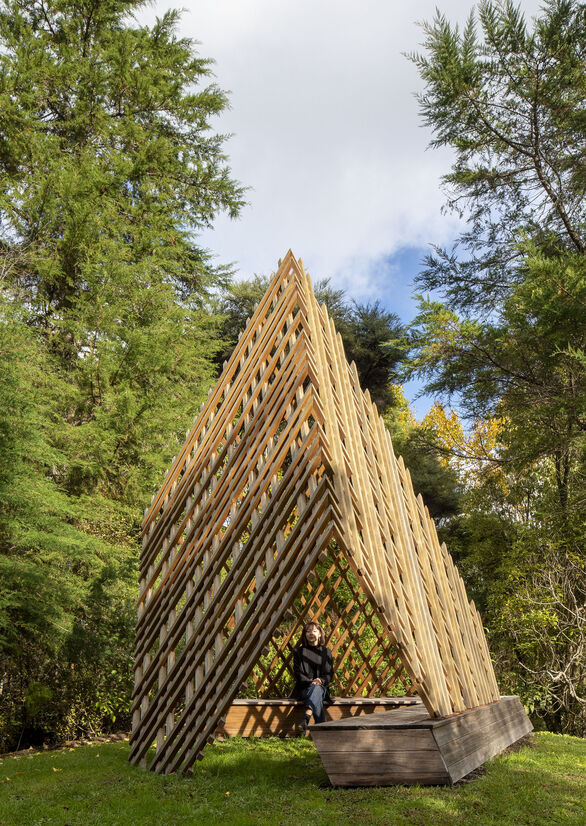
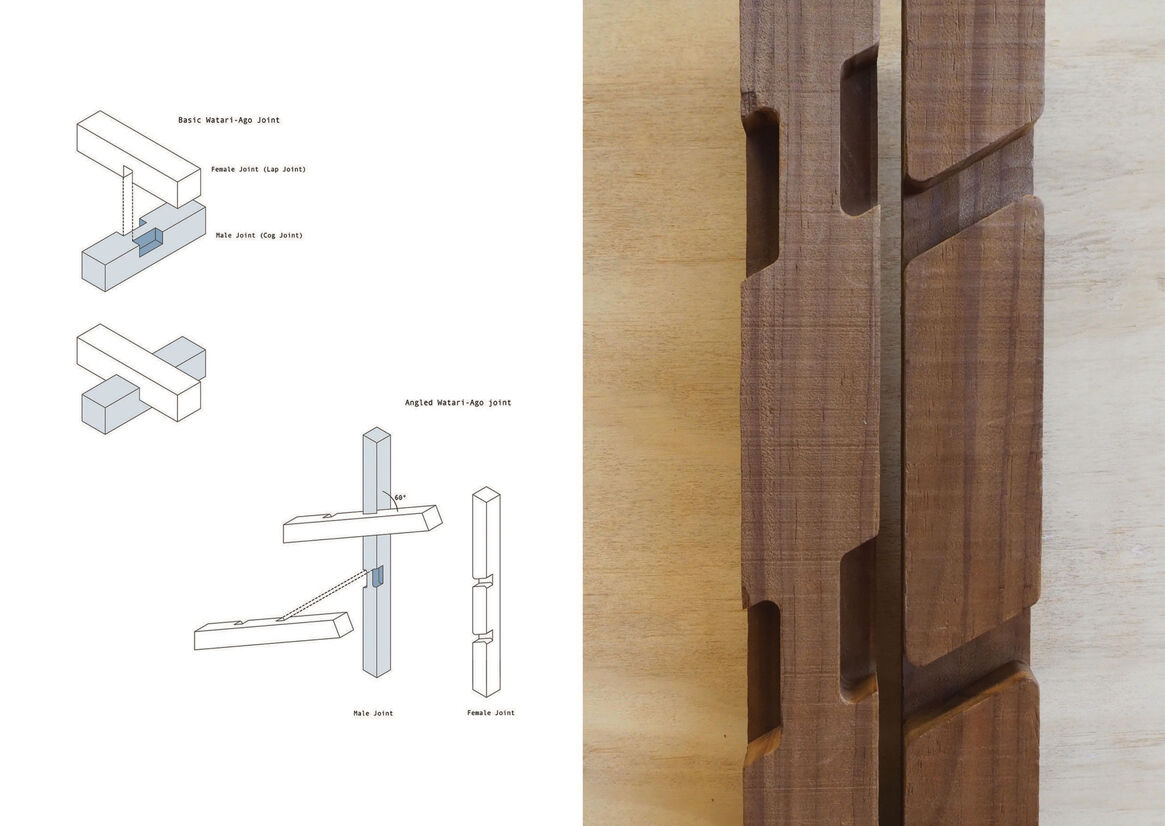
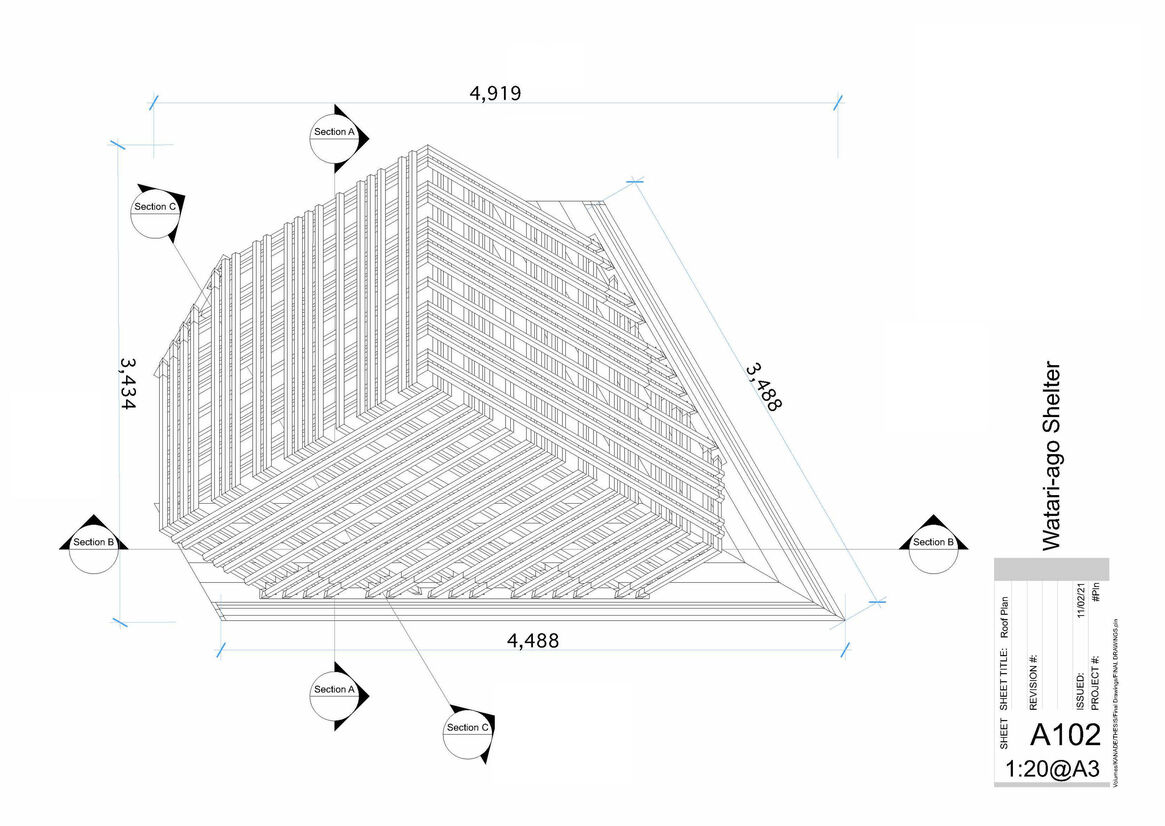
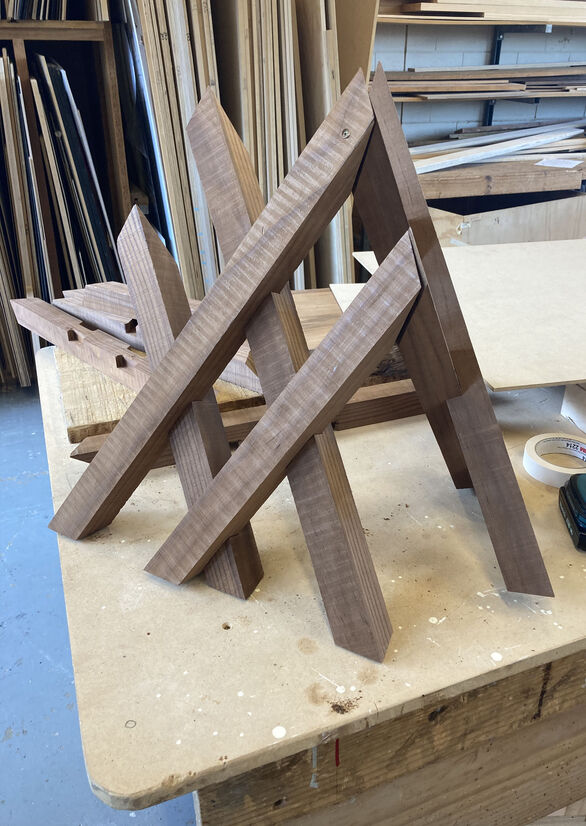
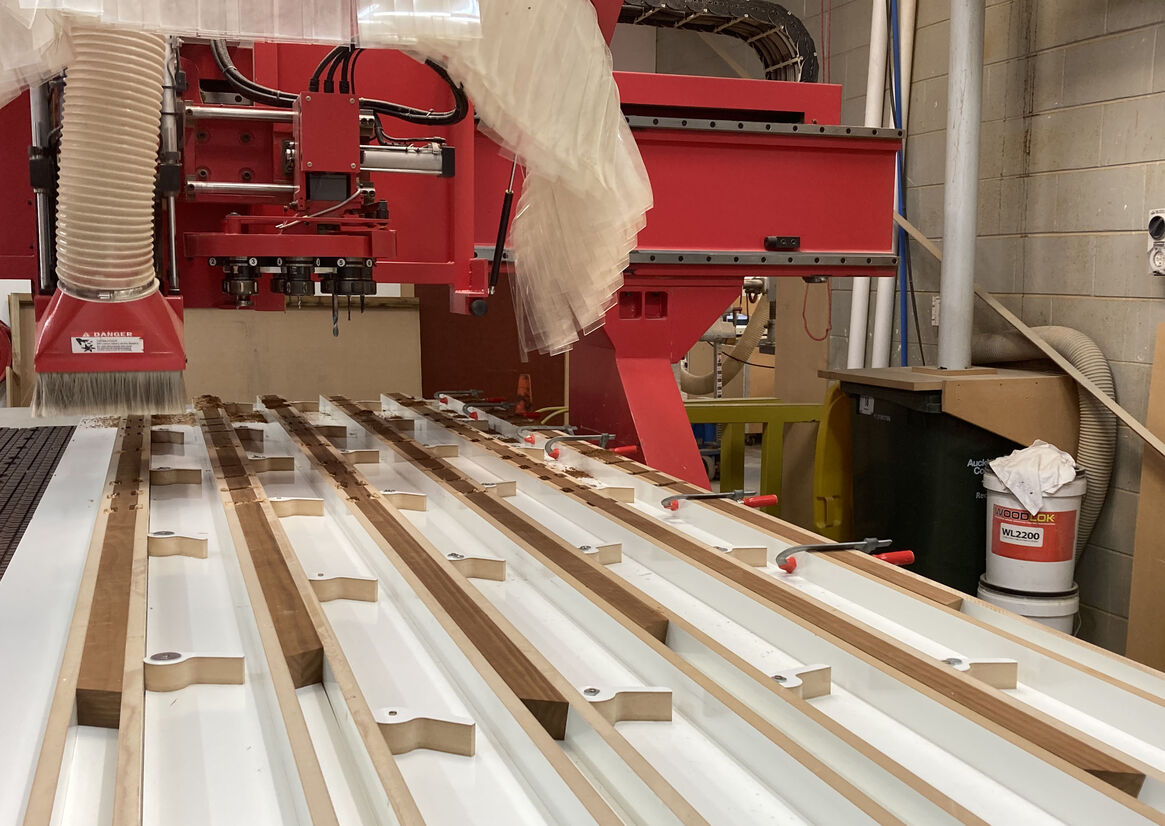
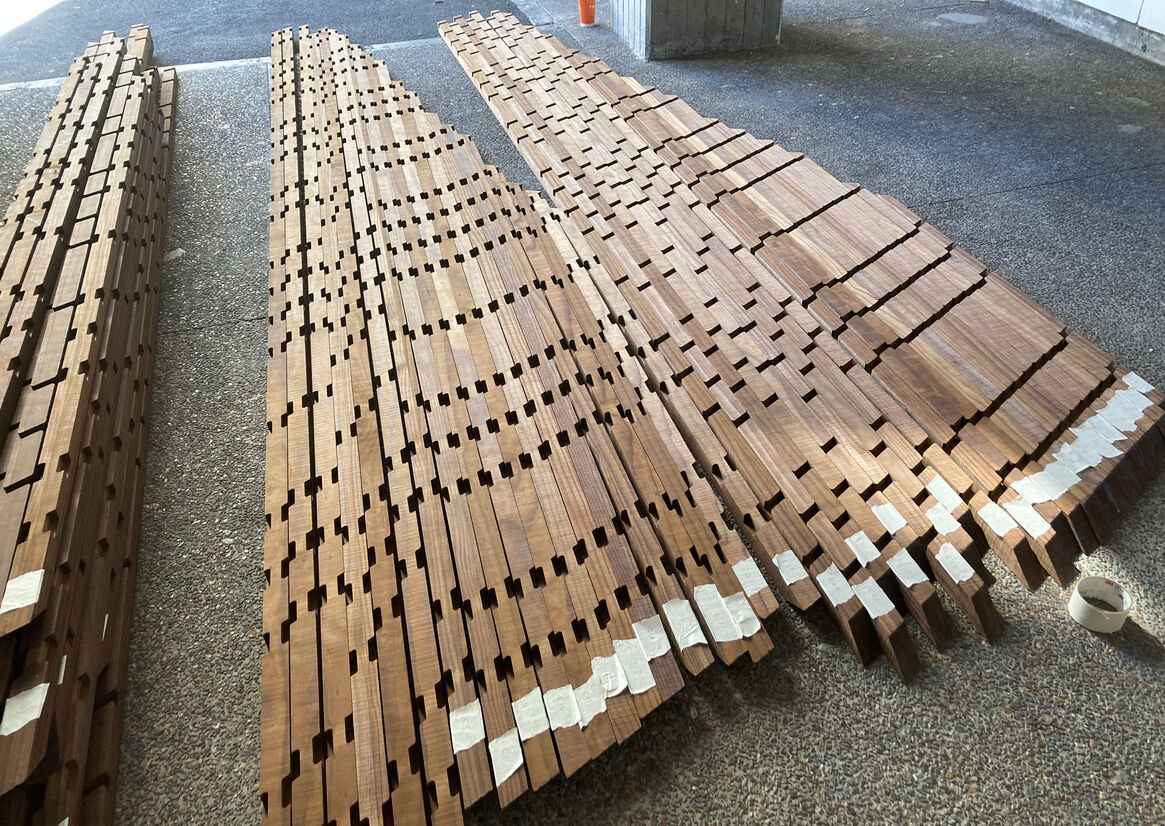
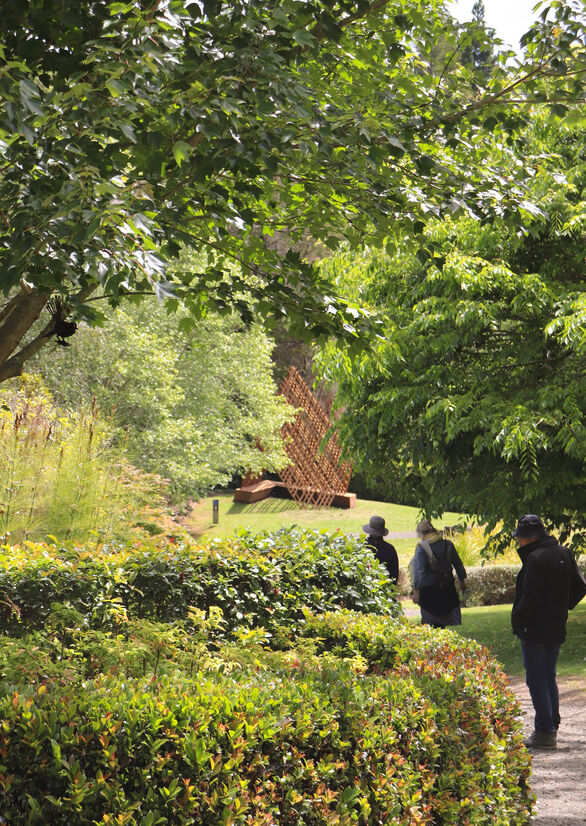
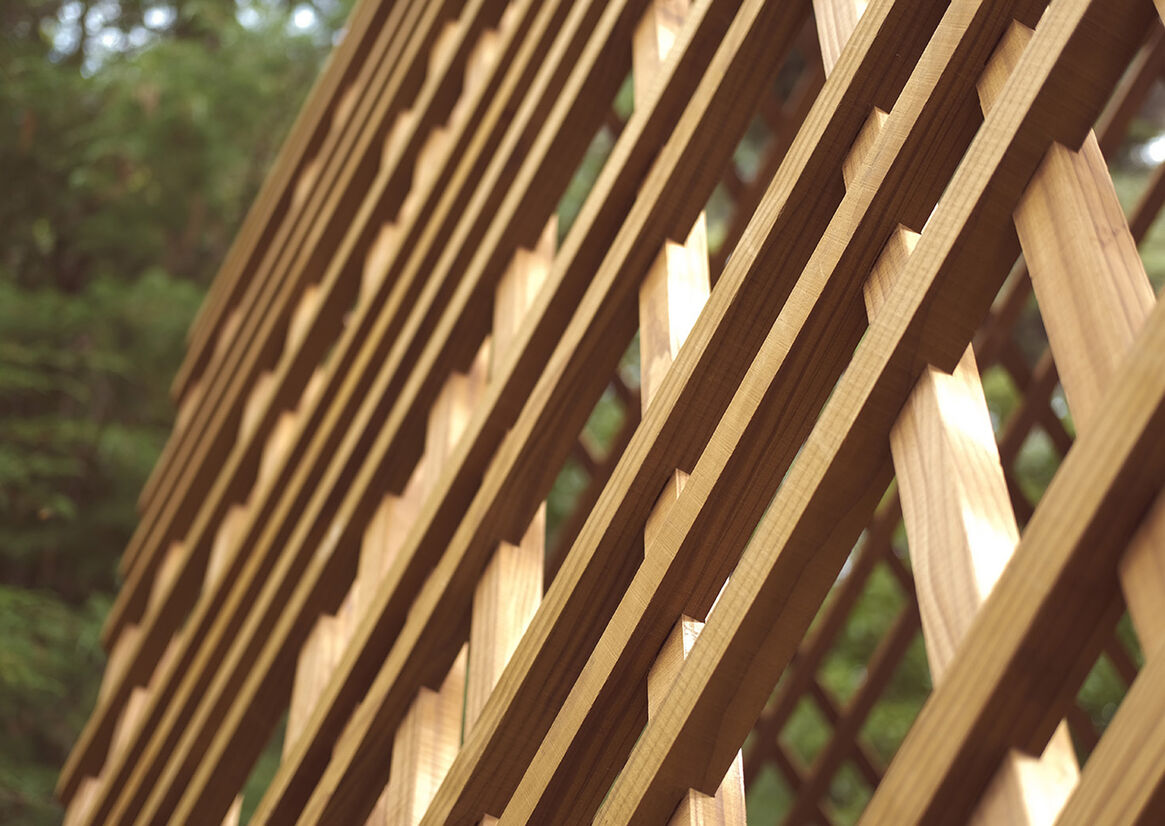
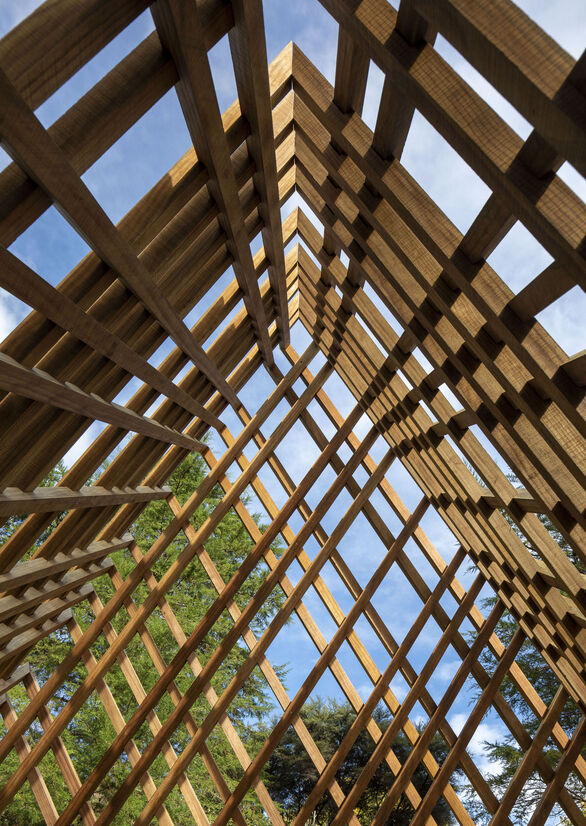

Description:
This structure forms part of an ongoing research project that seeks to expand the potential of existing digital fabrication tools for timber construction. The currently available technology consists of huge, highly sophisticated machines developed to mill large timber elements, while smaller milling machines tools are largely limited to cutting sheet materials and small custom-designed items. This project addresses the gap between these two scales by fine-tuning a method for using a standard three-axis flat-bed milling machine to mill sophisticated solid timber structural elements that would otherwise require an expensive and time-consuming process. This method was refined through numerous trials, with the Watari-Ago Shelter being fabricated as a full-scale demonstration of the techniques.
With the intention of expanding on previous research, this design is focused on a jointing technique drawn from traditional Japanese timber construction—a cogged lap joint called the watari-ago. It is naturally stronger than standard cross lap joints as less timber is cut from the timber. The watari-ago is traditionally used perpendicular, usually being used in roof trusses, but was employed in this project for its potential to be used on an angle, such that it also provides structural bracing. Derived from this simple joint, patterned lattice walls with compound cut ends are used to form a truncated triangular pyramid.
The structure was ruthlessly systematized, being reduced to just three details: the watari-ago interlocking joint, a corner joint, and a base detail were the structure meets the ground. Further, the lattice is set out on a repeating pattern, with the structural lines from outside of one wall, tucking under to become the inside of the adjacent wall. The individual elements of the structure have a high degree of resemblance, but the overall geometry of the irregularly truncated pyramid makes this pattern almost impossible to spot. This simplification allowed energy to be focused on refining the milling processes.
For millings machine to operate effectively and achieve the required accuracy, timber must be firmly held in precisely the correct position every time it is milled. In order to facilitate this, a jig was designed to secure the timber in place on the machine bed. A special clamp was developed—and milled using the machine it was later applied to—so that the deceptively simple jig ‘sandwiches’ the timber, a system which can be easily adapted to suit different timber shapes, types and cuts. The innovative jig and clamp system allows the timber to be accurately but rapidly loaded and unloaded, vastly simplifying and speeding up otherwise difficult milling processes.
For the finished structure, the joints were able to be milled so accurately that the walls are held together only by the friction in the joints, and the structure uses only a handful of screws. A single screw secures each ‘fold’ joint, and a line of screws was placed down the center of each wall purely for safety during erection.
The structure is currently part of the 2021 Kaipara Coast Sculptural Exhibition.