Product
Matt Mcgowan Easy Prosthetics - Additively Manufactured solutions for the Prosthetic Industry.
-
Tauira / Student
Matt Mcgowan -
Kaitautoko / Contributor
Aaron Johnston -
Kaiako / Lecturers
Bernard Guy, Simon Fraser
-
Client
NZLAS ( New Zealand Artificial Limbs Service) -
School
Victoria University of Wellington, School of Design
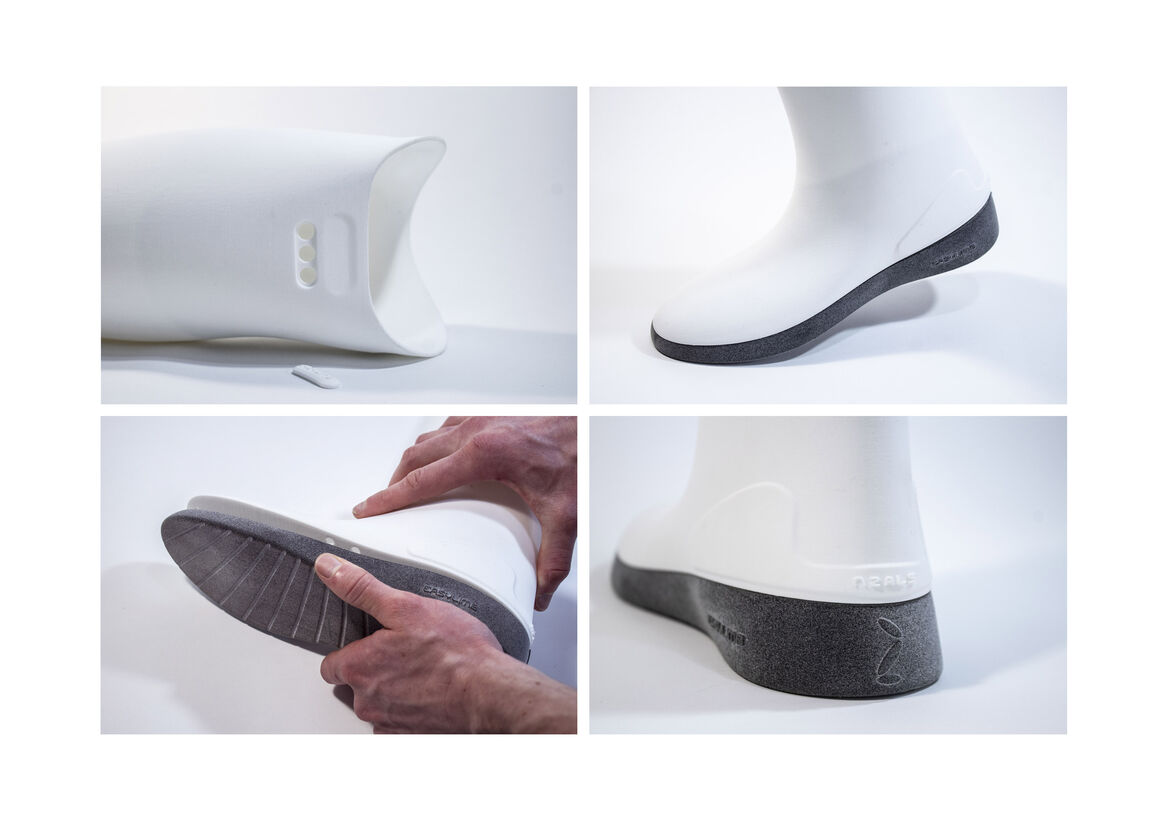

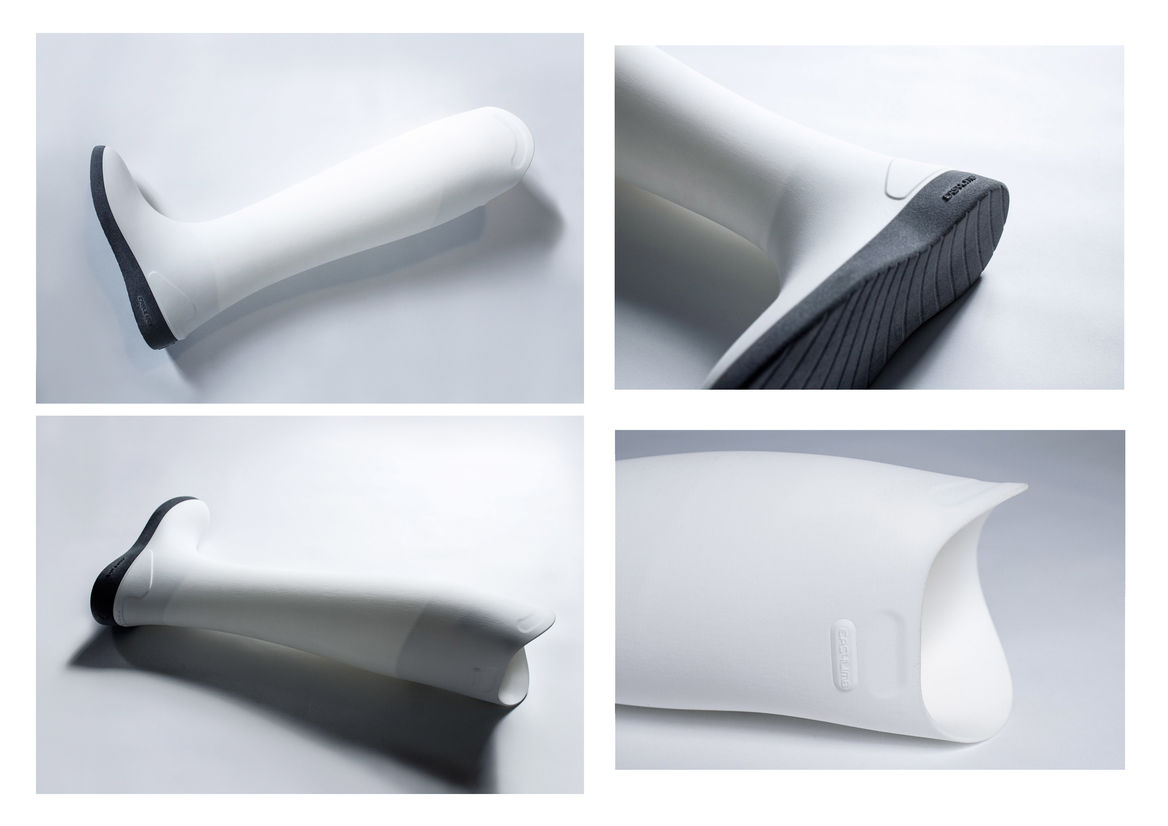
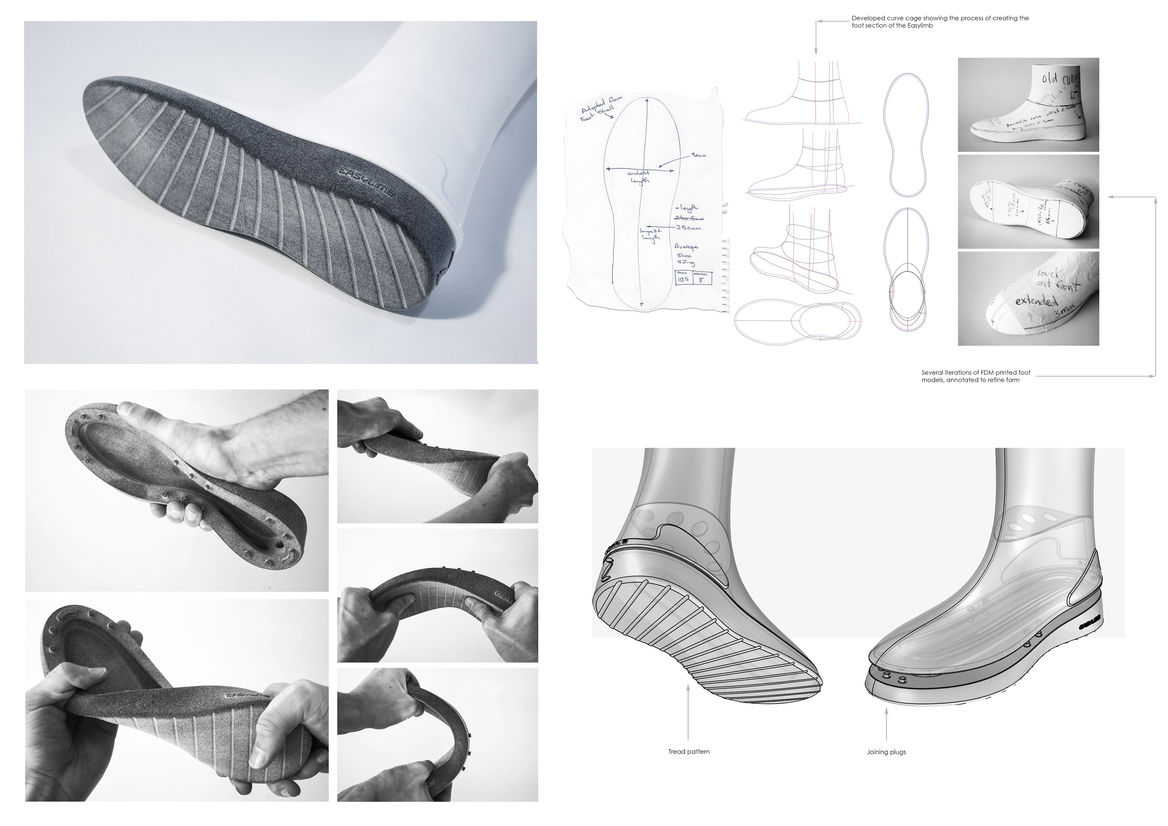
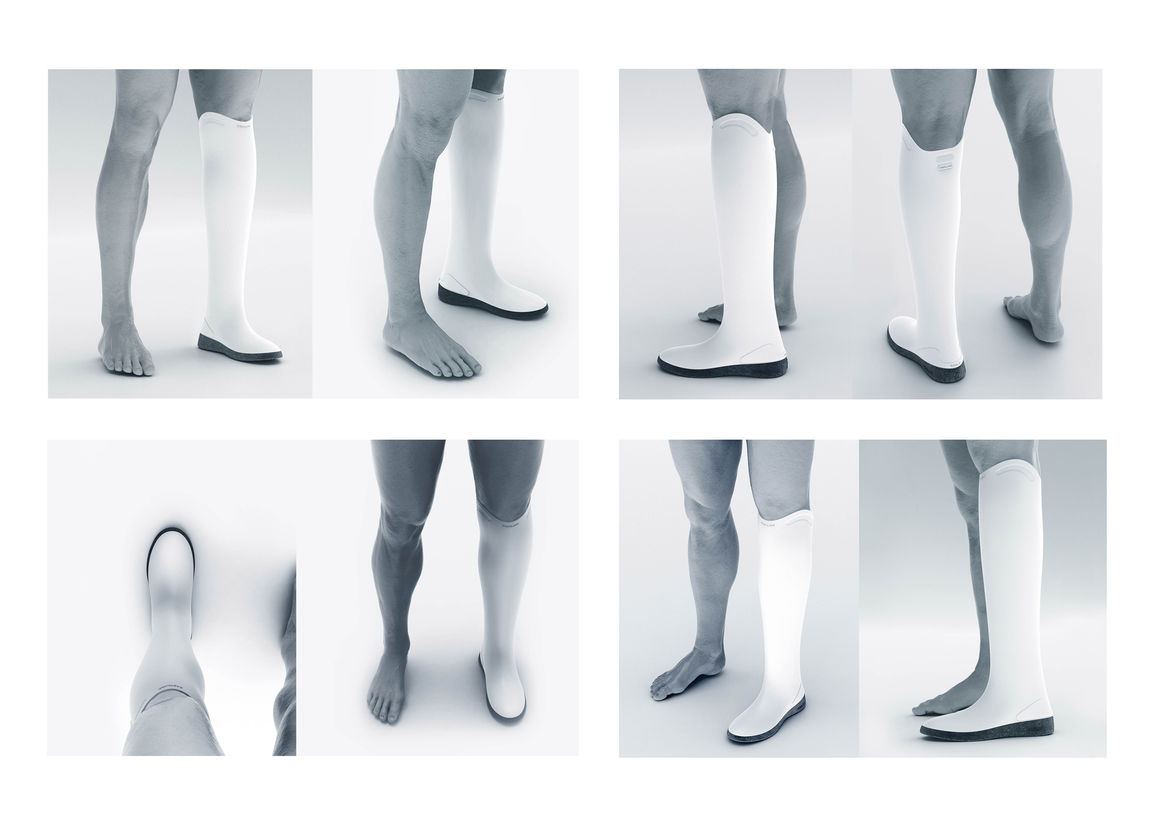
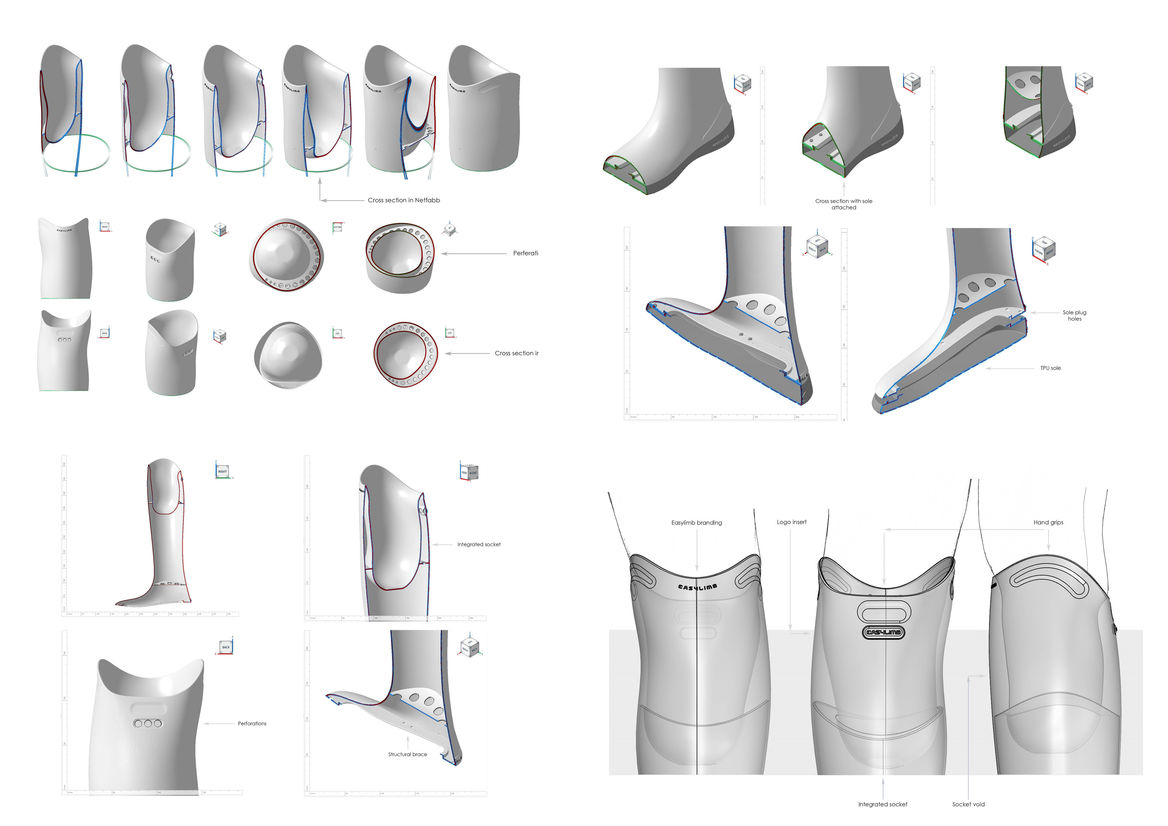
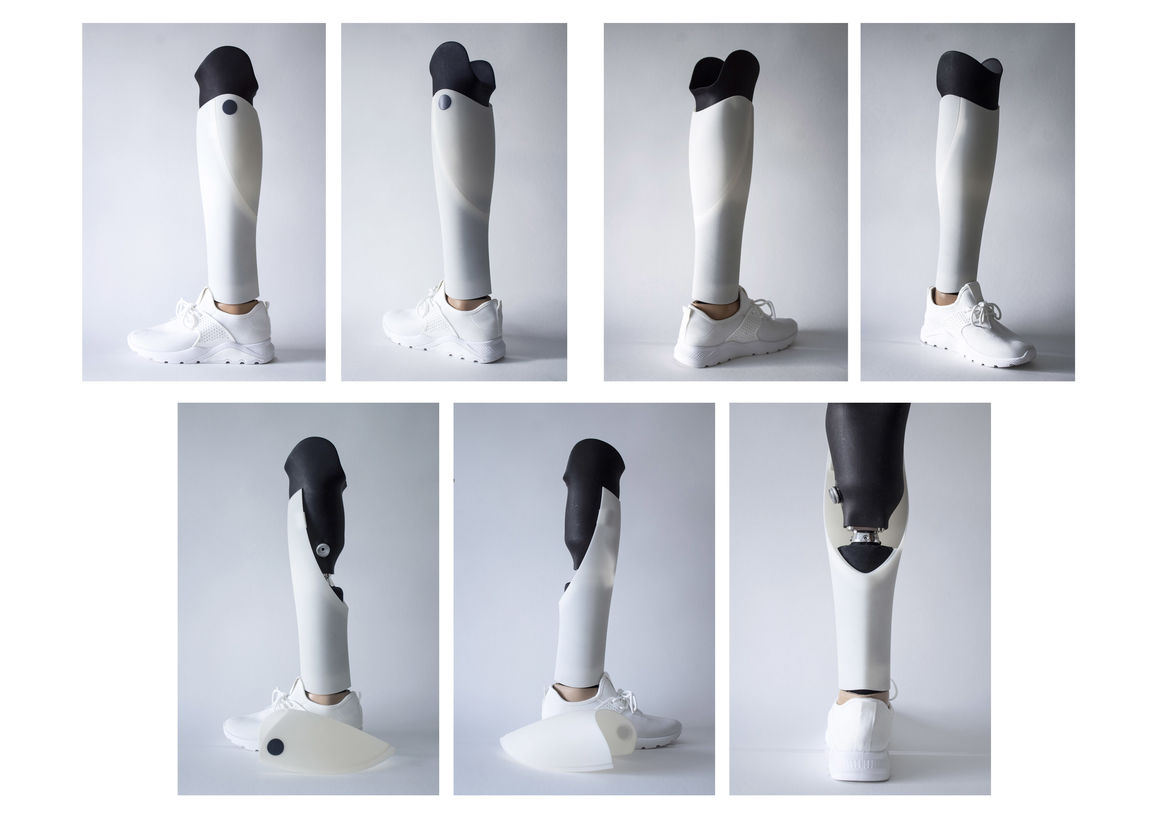
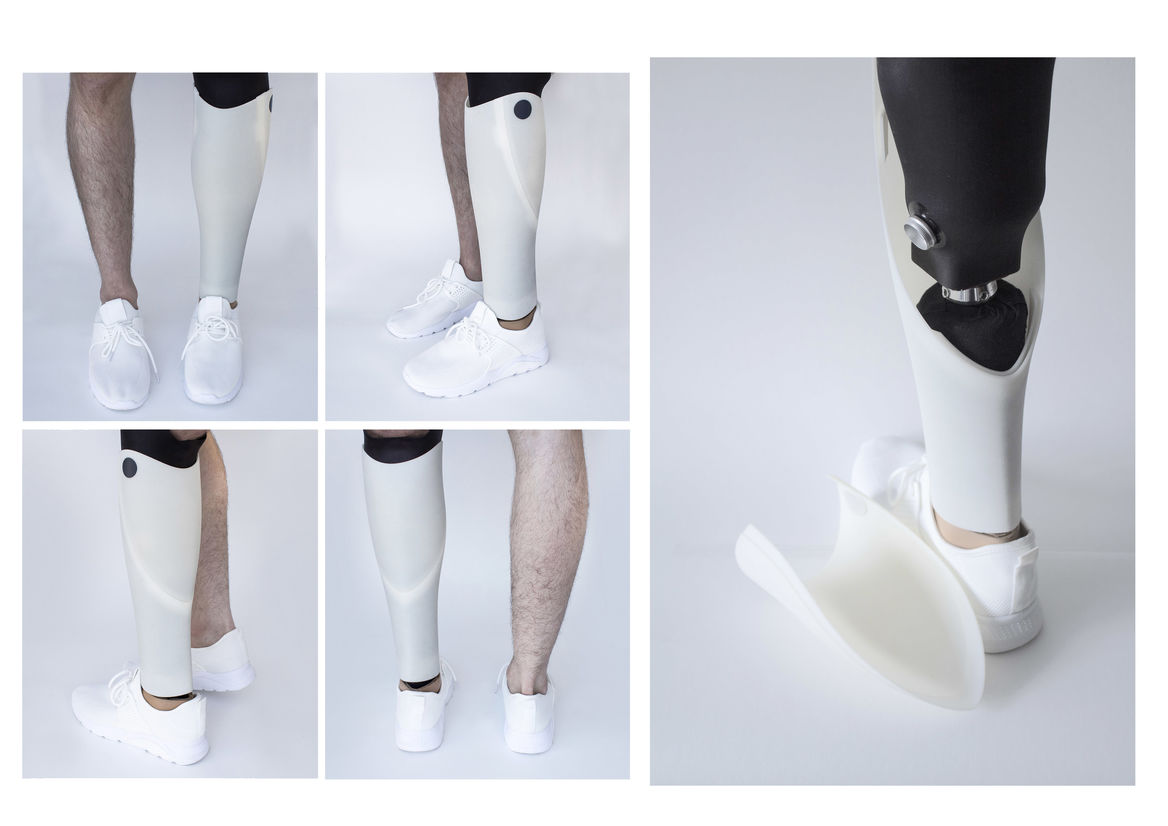
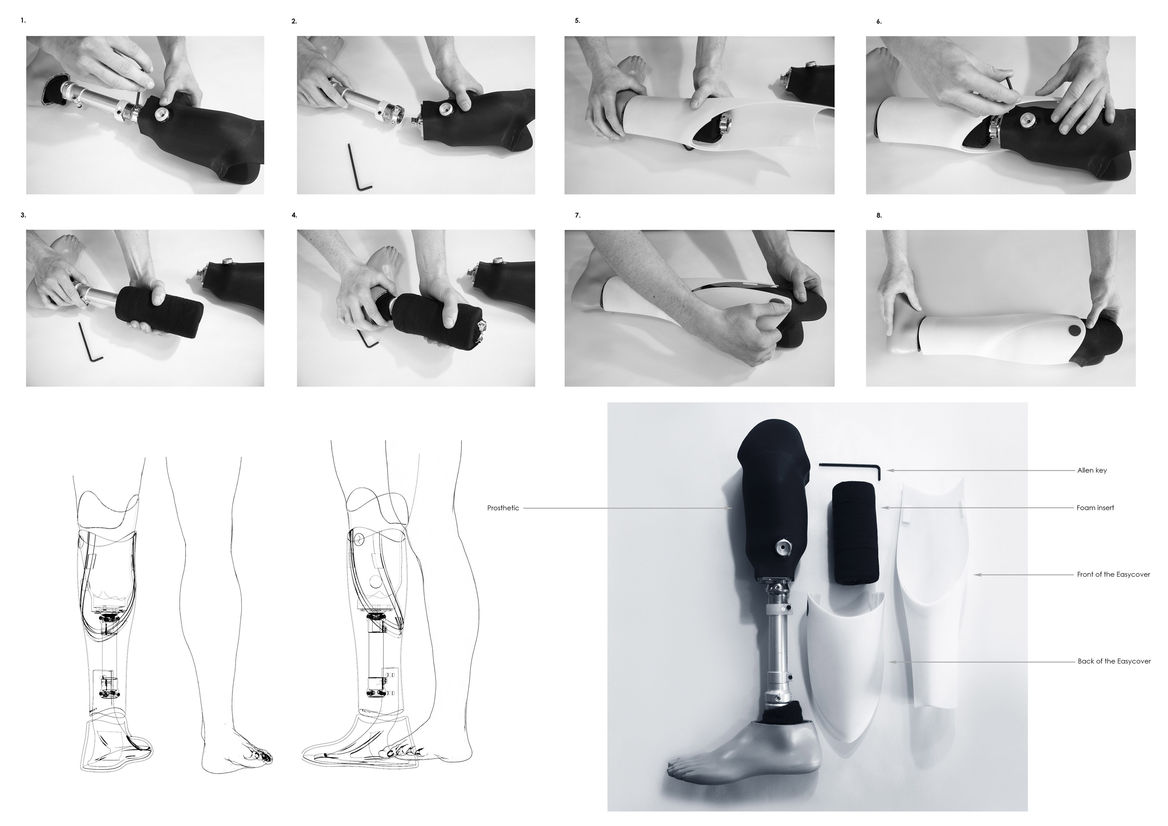
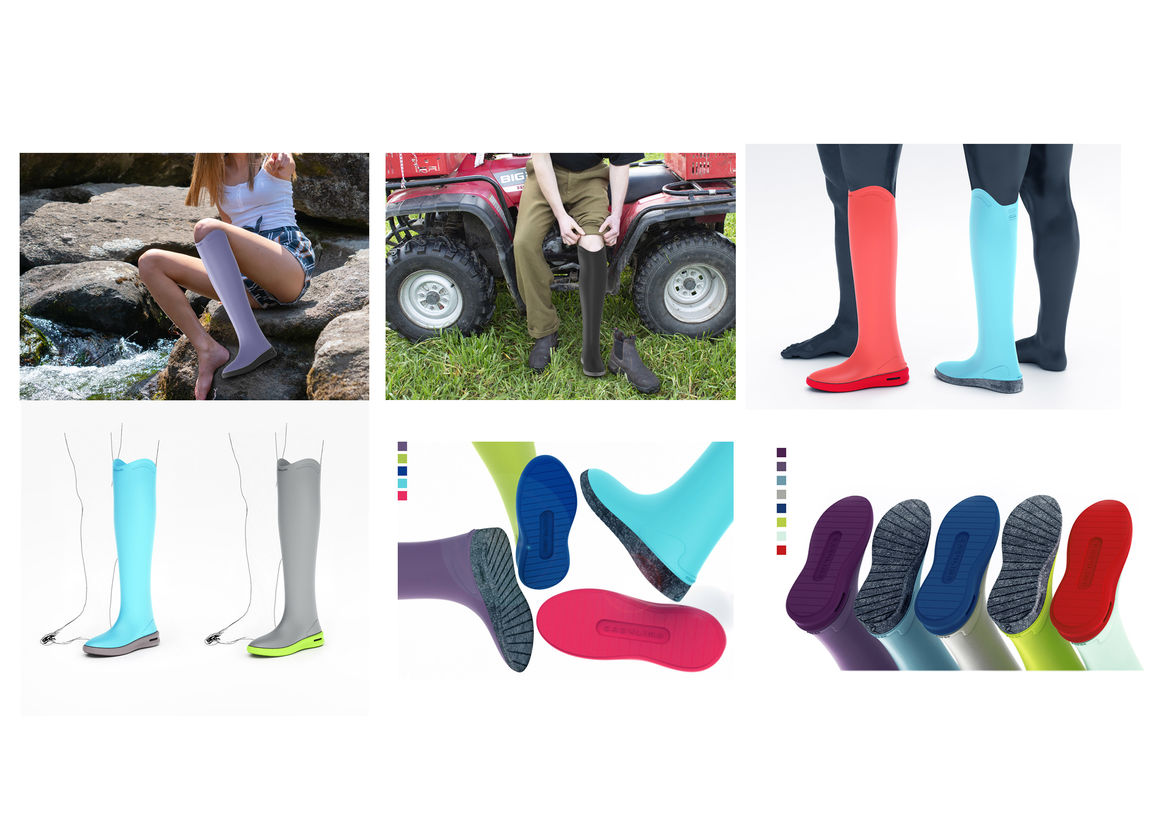
Description:
The Easylimb and Easycover were two product concepts created during a personal Masters thesis in 2020, in collaboration with the NZLAS.
The design process saw the creation of two prosthetic products.
Firstly, a below-the- knee Prosthetic Fairing (Easycover), and secondly, a fully 3D printed below-the- knee prosthetic (Easylimb).
To provide context for these products, it was found that for the prosthetic service industry, prosthetic design has largely skipped the mechanisation and mass production paradigm seen in the automation of consumer production. This industry still predominantly uses traditional hand fabrication methods to produce prosthetics as a one-off appendage.
These products and the research undertaken hoped to provide examples to the NZLAS (and the wider prosthetic service industry) how viable Additive Manufacture could be within its prosthetic production. It illustrated how AM production could allow amputee’s diagnostic data (including the socket) to be integrated into products themselves. This aimed to allow for further opportunities for product development, moving away from the prosthetic socket being one component amongst many in a one-off appendage.
This research and subsequent products strived to argue for the value of design. This was achieved by considering a broad base of users, resulting in concepts that sought a wider appeal. This aimed to move away from the one-off bespoke appendage. which was, and still is the precedent in the current environment.
This research investigated emerging platforms of manufacturing in both Digital and Additive Manufacturing (3D printing), with the development of the designs in this project focused on brand, client and company identity. This focus addressed the integration of an Industry 4.0 model in favour of the amputee client, and realised future outlooks of prosthetic production envisioned by the NZLAS.
This research and products created aimed to propose the question; how can design communicate the possibilities of Additive Manufacture?
The research undertaken within this project aimed to illustrate the importance of creating tangible and readymade products. This aimed to allow the NZALS, it’s staff and amputee clientele, to understand the benefits of design, branding, and emerging platforms of manufacture in the production of prosthetic diversity.
Product descriptions:
Easylimb:
The Easylimb prosthesis aims to integrate the scanned prosthetic socket of an amputee and combine it with additional CAD modelling to create an all-in-one daily activity limb. The goal was to produce a full-length, lower-limb prosthesis which could be produced with Additive Manufacture, as one singular model with no external componentry, using Muti-jet Fusion or selective laser sintering technologies. The aim for the Easylimb is to address amputee accessibility through a secondary prosthetic limb. The Easylimb aims to be low-maintenance, user friendly and care free to use in everyday activities.
“The Easylimb is beneficial to user groups that are looking for a modern and stylish below knee exoskeleton limb for everyday activity. Key aspects that make this great for the wider patient groups are this limb has fewer limitations, less ambiguity, fuss and parts.” (Aaron Johnston, NZLAS Prosthetic Technician 2020)
Easycover:
The Easycover is an easy access prosthetic Fairing manufactured using SLS 3D printing technology. The Fairing aims to incorporate diagnostic data from the amputee to create a product that fits snugly around the circumference of the amputee's socket. It also ensures the product is anatomically proportionate to the amputee's existing biological limb. The fitting system, via the use of a foam insert, and the products split design, make the fitting of the Easycover to the prosthetic potentially more efficient and less difficult than existing designs.
For further information and images please visit https://www.mattmcgowandesign.com/
Judge's comments:
The high level of design research, technical development and aesthetic resolution was admired by the judges who also appreciated the application of additive manufacturing to this challenging individually focused field of design.